Heat exchanger tube and tube plate expansion process---Refrigeration technology
According to the use conditions of the heat exchanger, the processing conditions are different, the connection method is basically divided into expansion, welding, expansion and welding combination of three, because the expansion method can withstand higher pressure, especially suitable for poor material weldability and the manufacturer's welding workload is too large. Therefore, this method is widely used in practical production. With the continuous development of technology, new processes such as roller expansion tube, explosive expansion tube and hydraulic, liquid bag and rubber expansion tube have been developed successively. This paper intends to compare these several kinds of tube expansion technology to provide a reference for the selection of reasonable tube expansion technology in actual production.
Traditional expansion process
1. Roller expansion method
This method is to embed three small-diameter rollers on a frame, and a tube expander with a conical mandrel in the middle. When expanding the tube, the cylindrical part of the tube expander is inserted into the tube hole, and the mandrel is rotated by electric, pneumatic or other power. The roller rotates along the circumference of the mandrel, so that the mandrel is squeezed into the inner surface of the tube and forced to expand the tube to reach a certain degree of expansion, so that the tube is tightly expanded on the hole of the tube sheet. The tube expansion operation can be divided into two types: forward and backward. The forward type is to insert the frame into the tube, rotate the mandrel, and expand it forward. After reaching the specified tightness, the motor reverses and pulls it out of the tube to complete the tube expansion process. The reverse type is the same as the forward type. The mandrel rotates forward. After reaching the original tightness, the motor stops, and the clutch of the backward device engages and reverses. The relative position of the roller and the mandrel remains unchanged. While reversing, the tube is expanded continuously and evenly from the depth to the entrance. Since this expansion process is from the inside to the outside, the elongation of the tube occurs on the outside of the tube sheet, which can eliminate the stress state of the tube bundle and improve product quality. Therefore, it is used for connections with an expansion length greater than 60 cm.
2. Explosive tube expansion process
This method uses high-energy explosives to generate a huge pressure of shock waves at the moment of explosion (10×10-6~12×10-6s), forcing the tube to produce high-speed plastic deformation, thereby expanding the tube and the tube sheet together to achieve the connection between the tube and the tube sheet. The columnar explosive is placed at the center of the tube end. To prevent the shock wave from damaging the tube wall, there is a tubular buffer filler (viscous or plastic) around the explosive so that the pressure can be evenly transmitted to the tube wall.
New expansion technology
1. Hydraulic expansion technology
Hydraulic expansion technology is also called soft expansion, which can expand more pipe joints at one time. Hydraulic expansion is a new expansion technology. It applies high hydraulic pressure to the inner surface of the pipe to make the pipe plastically deform and expand it to the inner surface of the plate hole. The expansion head of hydraulic expansion is a mandrel with a diameter slightly smaller than the inner diameter of the pipe. There are multiple seals on the outer surface of both ends of the mandrel. There is an oil inlet hole in the middle of the mandrel. High pressure is applied to the pipe section between the two seals to make the pipe plastically expand and deform to achieve expansion.
2. Rubber expansion technology
The new rubber expansion technology is developed on the basis of rubber deformation under stress. It uses the radial pressure generated by the axial compression of the rubber elastic body to expand the pipe to the tube sheet. The working principle of the rubber expansion machine is that when the loading rod applies tension, the expansion rubber is axially compressed and radially expanded at the same time. The expansion force is sufficient to deform the pipe material, thereby realizing the connection between the pipe and the tube sheet. To prevent the axial movement of the rubber under high pressure, special hard rubber sealing rings are installed at both ends of the expansion head. The pull rod of the rubber expansion tube is made of high-strength steel. It is loaded on the pull rod by water or oil with a pressure of about 20MPa. Since the tension is balanced by the back pressure ring, it forms an internal force system without other support or constraints. The expansion rubber is made of materials with high elasticity and strength.
Comparison of several expansion process methods
1. Analysis of the advantages and disadvantages of mechanical expansion process
Mechanical expansion is completed by using an expander. The expander is divided into two types: forward expansion and backward expansion according to the different feeding directions. The former is suitable for general heat exchangers and expansion of tubes with a hole diameter less than φ38mm. Its expansion rod has a taper of 1:25 to 1:50, which makes the circumferential force less than the friction force, thereby avoiding the relative sliding between the roller and the expansion rod. In order to facilitate the introduction of the expander, the roller is designed with a head end with a certain taper; the latter is usually used for deep expansion and expansion with a diameter greater than φ38mm. The radial expansion of the roller is achieved by the backward pulling force of the expansion rod. When expanding the tube, the tube is axially elongated, so it can be deformed freely to the outer end, thus avoiding the axial compressive stress and deformation caused by the forward expander to the tube connection. Mechanical expansion can not only withstand a certain axial force, thermal shock and repeated thermal cycles, but also has simple operation and flexible use. It is widely used in manufacturing and maintenance. However, mechanical expansion also has the following disadvantages: the expansion between each tube is different, the connection strength and tightness are uneven; the inner surface of the expansion interface is hardened, which makes it difficult to repeat expansion. The compatibility of expansion of tube and tube sheet materials is limited to a certain extent, such as the expansion of titanium tube and carbon steel, aluminum tube and carbon steel, etc.; the labor productivity is low, and the expansion of small diameter or thick wall tubes is difficult.
2. Comparative analysis of other expansion processes and mechanical expansion processes
In addition to the advantages of uniform force on the tube wall, less axial elongation of the tube and uniform work hardening, hydraulic expansion has a large axial pull-off force and good sealing because the metal of the tube wall can almost completely fill the tube hole groove. Advantages of rubber expansion tube: It belongs to the expansion process of soft characteristics. The boundary between the expansion zone and the non-expanded zone is not obvious, the transition is smooth, the residual stress is small, and the performance of stress corrosion and fatigue resistance is good; there is no axial extension of the tube, and it is suitable for welding before expansion like the explosive expansion tube; the pipe diameter deviation requirement is not strict, and it is suitable for the expansion of elliptical tubes; the application range is large, and the diameter of the tube of φ10~φ100mm and the thin-walled tube of 1mm can be well expanded; the hydraulic control pull rod is easy to control the quality of the expansion tube and adjust the expansion tightness. The basic requirement of explosive expansion is only to expand the tube to the tube sheet and ensure sufficient connection strength. Therefore, for the expansion of commonly used specifications of heat exchanger tubes, most of them use low explosion velocity explosives such as ammonium nitrate, and the amount of explosives is small, so ordinary expansion tubes can also be directly expanded with detonators or detonating cords, and the tube wall is protected by kraft paper. Because the tube is in an instantaneous superplastic state under huge pressure during the explosion, it can fully fill the hole groove, so the explosive expansion tube has a higher connection strength and reliable sealing; because the explosive expansion tube has good material compatibility, it is suitable for expansion of various diameters of different materials; in addition, the explosive expansion tube has another significant advantage, that is, the process tooling is simple and the production efficiency is extremely high. However, there are certain limitations on the compatibility of the expansion of the tube and the tube sheet material, such as the expansion of titanium tube and carbon steel.
Conclusion
(1) To ensure the reliability of the connection between the tube and the tube sheet, it is not only required to correctly and reasonably select the connection form according to the design conditions (such as temperature, pressure, joint connection strength, fatigue and medium corrosiveness, etc.), but also to have a reasonable process system and inspection system suitable for different connection forms during manufacturing and construction. Practice has proved that the reliability of the connection joint is not only determined by the design conditions, but also often affected by the feasibility of manufacturing and construction.
(2) Among several expansion tube processes, rubber expansion tube and hydraulic expansion tube are the best in terms of expansion performance; explosive expansion tube has the highest production efficiency; due to the limitation of production conditions, mechanical expansion tube is currently the most commonly used.
(3) In the process of processing the connection between the heat exchanger tube and the tube sheet, if only expansion is required, the expansion tube process method with better expansion performance should be selected as much as possible according to the actual production conditions to ensure the excellent expansion quality.
(4) For occasions with harsh use conditions, such as heat exchangers that are resistant to high temperature and high pressure, dynamic load and corrosion, a combination of expansion and welding should be used. Many experimental data show that no matter which expansion welding connection form is used, the tensile strength and sealing performance of the joint are higher than those of expansion or welding alone, and in some cases even exceed the strength of the tube material.
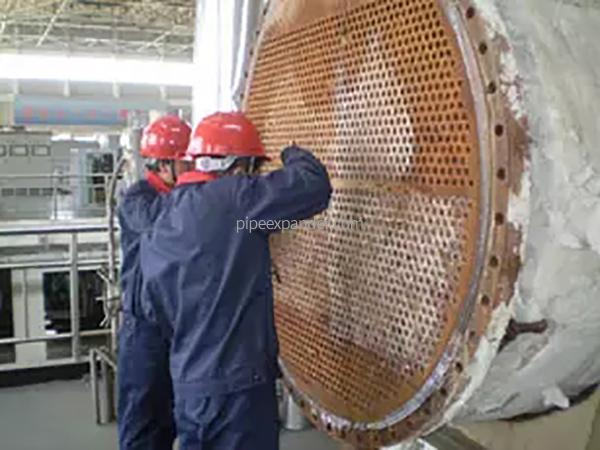